Multi-Camera
Technology
Unparalleled Robustness with Self Diagnosis and Camera Redundancy
Mapvision’s multi-camera technology allows the system to internally assess its measurement process by comparing results from various triangulations. Even if a camera is obstructed, the system can identify and isolate the issue while still delivering consistent results from other triangulations, ensuring reliable and uninterrupted performance at all times.
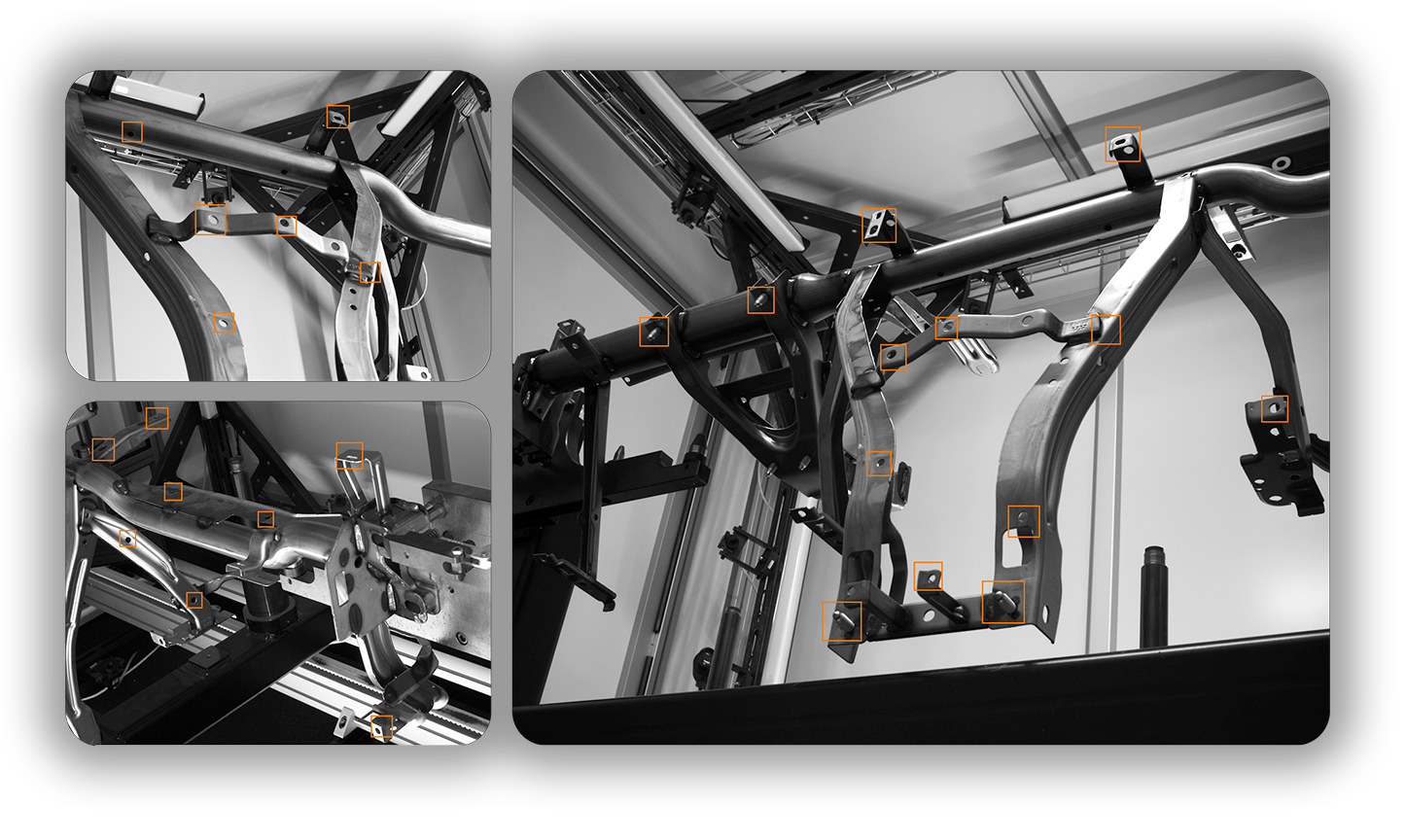
Multi-camera technology is a photography-based inspection solution that captures photographic data of the whole part and conducts all inspections and measurements directly on the images.
-
The Setup
-
Capture Images
-
Save to Database
-
Inspect Images
-
Analyze & Manage
-
Retroactive Inspection
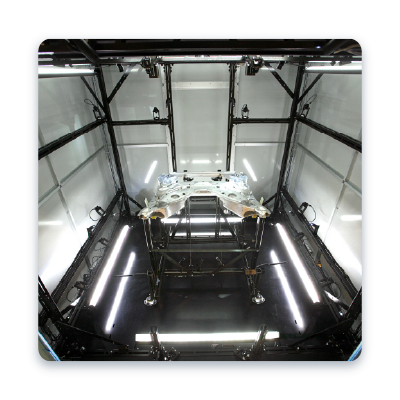
The Setup
The Mapvision Q-Series conducts dimensional measurement and presence check within a controlled environment. The enclosed inspection area shields against factory floor ambient light interference. The system employs dedicated lighting to ensures optimal illumination for image capture.
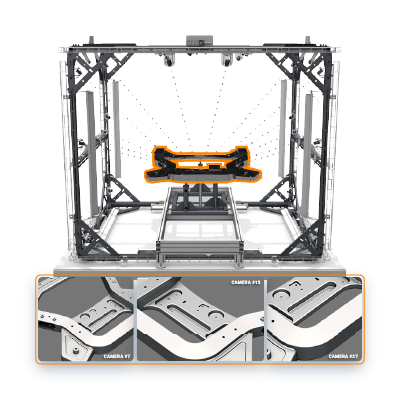
Capture Part Images
Fixed cameras capture high-resolution images of the part from all angles within a few seconds. This ensures that every part is documented, providing a complete data set for further analysis.
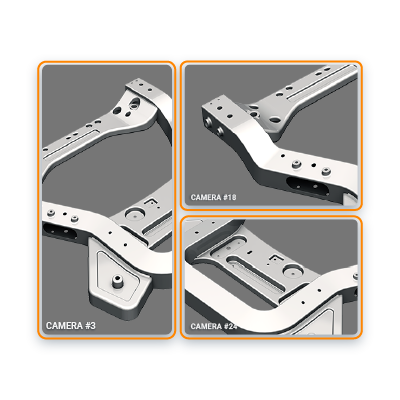
Saved Images to the Database
Images are saved to the image database of the measurement unit.
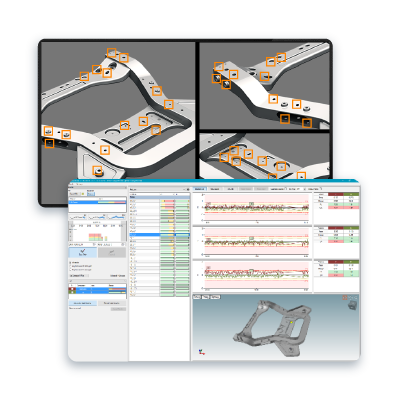
Inspect on the Images
Mapvision’s powerful machine vision and photogrammetry algorithms conduct geometric measurements and presence check directly on the collected images.
Results are made available in real-time to conduct deep-dive analysis. Users can adjust the measurement program, add new inspection points, and even manage the whole process remotely at any point.
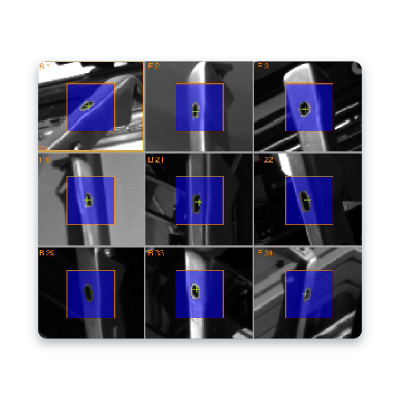
Analyze and Manage
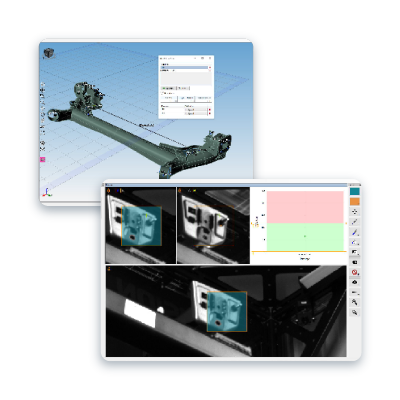
Retroactive Inspection
With part images stored in the database, you can inspect entirely new features or re-inspect the part based on modified specifications even after the parts have been processed. This reduces the need for manual sorting and eliminates the possibility of recalling entire batches.
From real-time inspection, to flexibility, programmability, and robustness. Multi-camera technology provides brand new capabilities that have not been available to conventional vision inspection systems—enabling manufacturers to enjoy the benefits of digitization.
Revolutionizing In-Line Inspection for Automotive Parts
Multi-camera technology is suitable for a wide range of automotive parts no matter how large or complex they are. From side beams and axles to cross car beams, underbodies, and EV battery modules; multi-camera technology provides unique benefits to take full control over quality and reduce costs.
-
EV Battery Tray
-
EV Battery Module
-
Cross Car Beam
-
Subframe
-
Body-in-White (BiW)
-
Other Use Cases
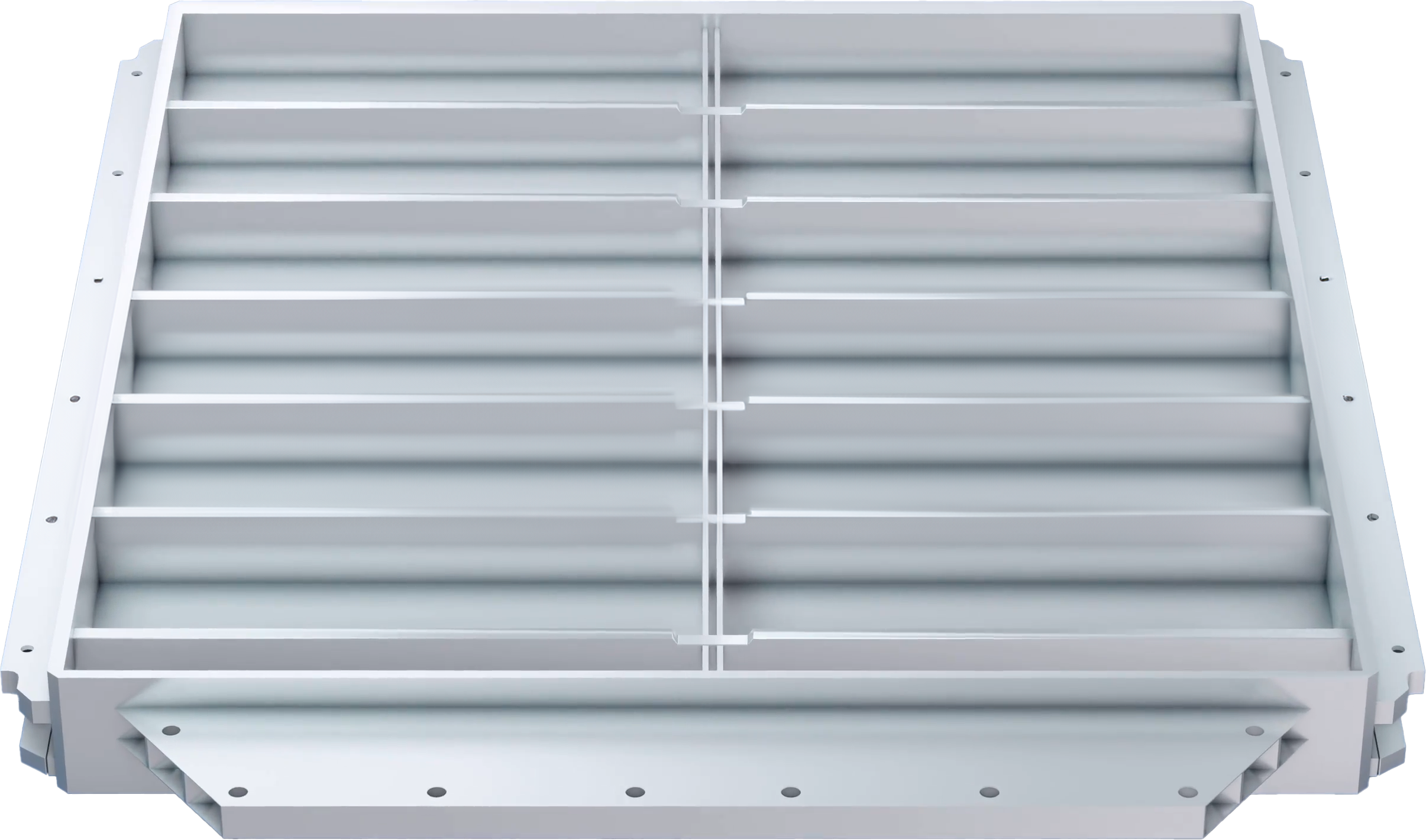
1200+
Features Inspected
30 Seconds
Inspection Time
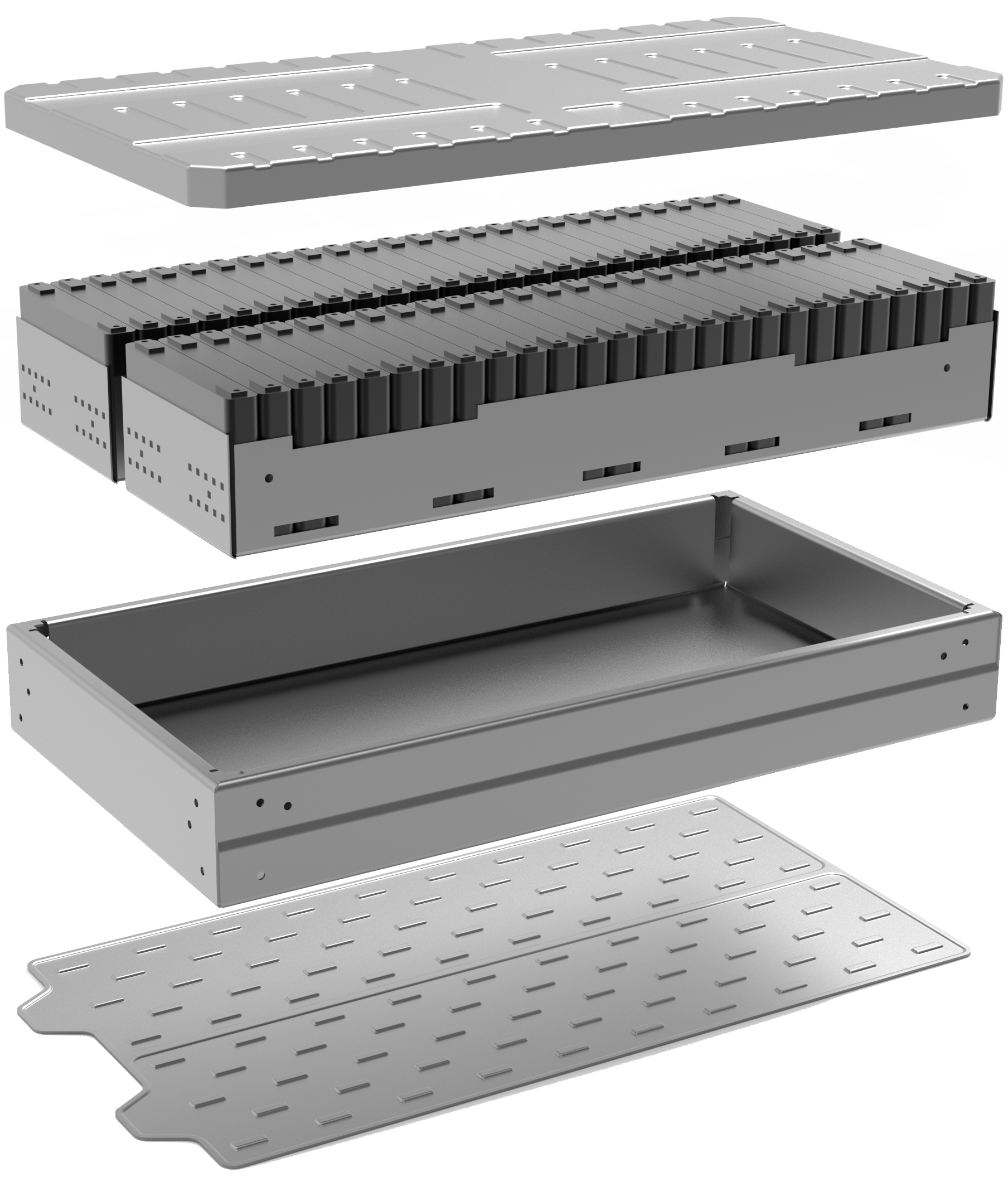
800+
Features Inspected
30 Seconds
Inspection Time
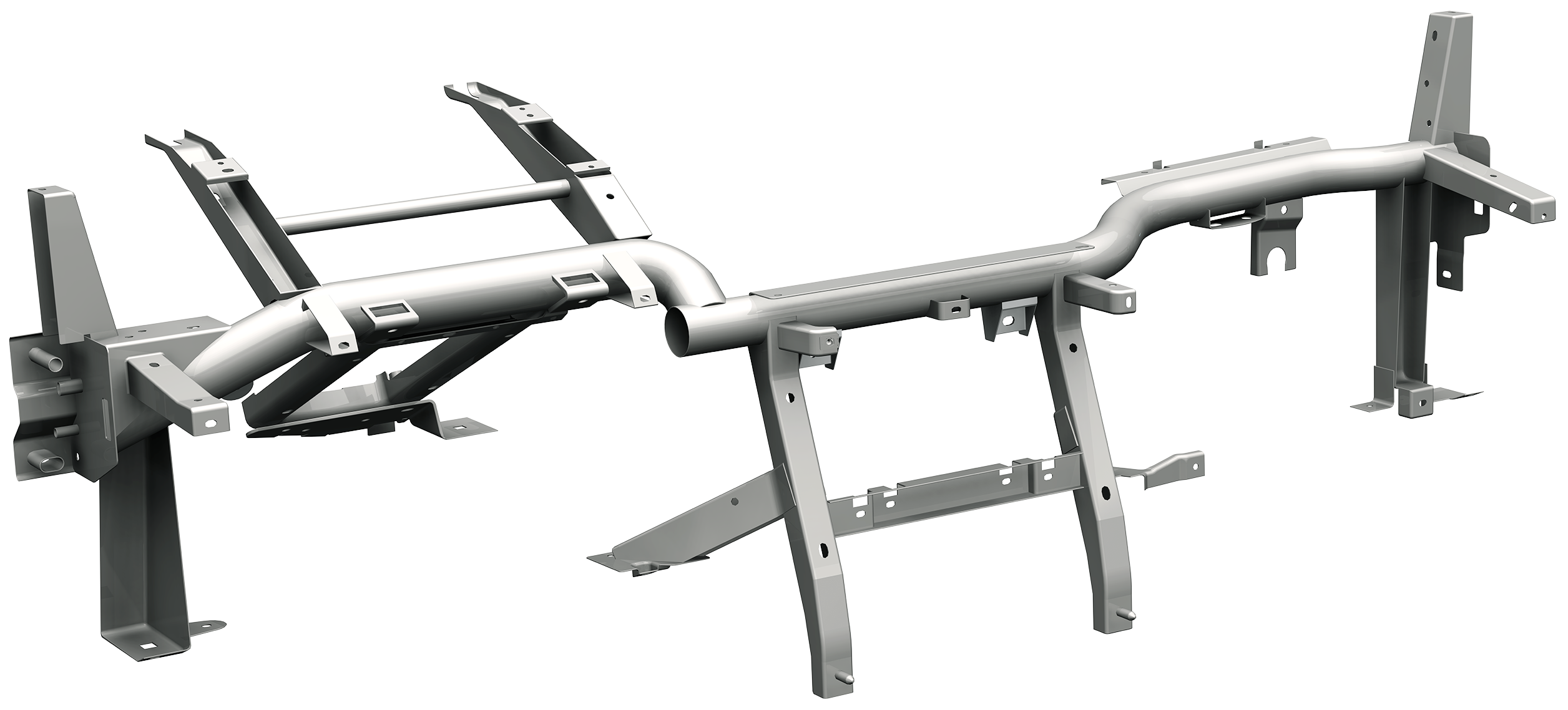
200+
Features Inspected
30 Seconds
Inspection Time
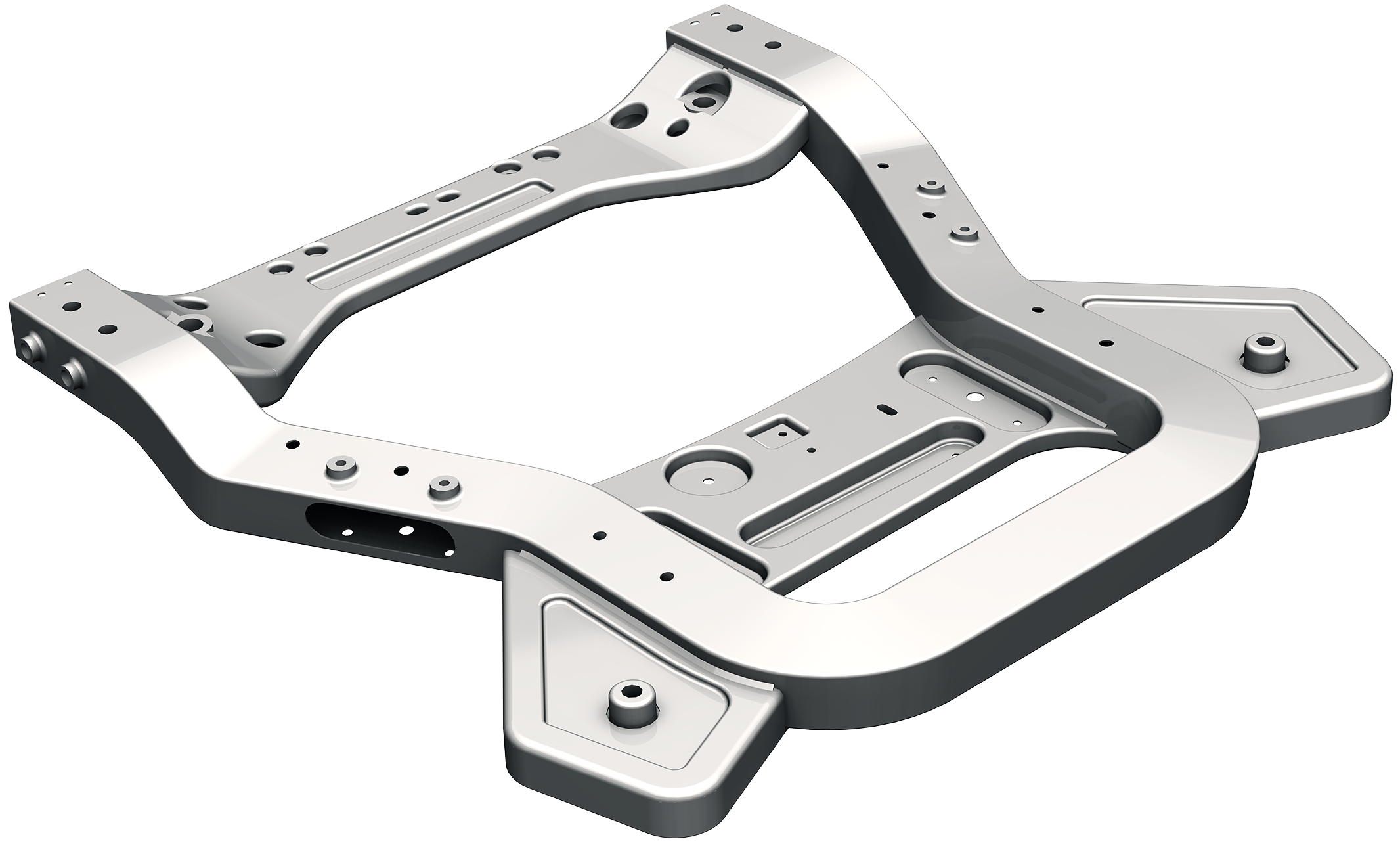
150+
Features Inspected
30 Seconds
Inspection Time
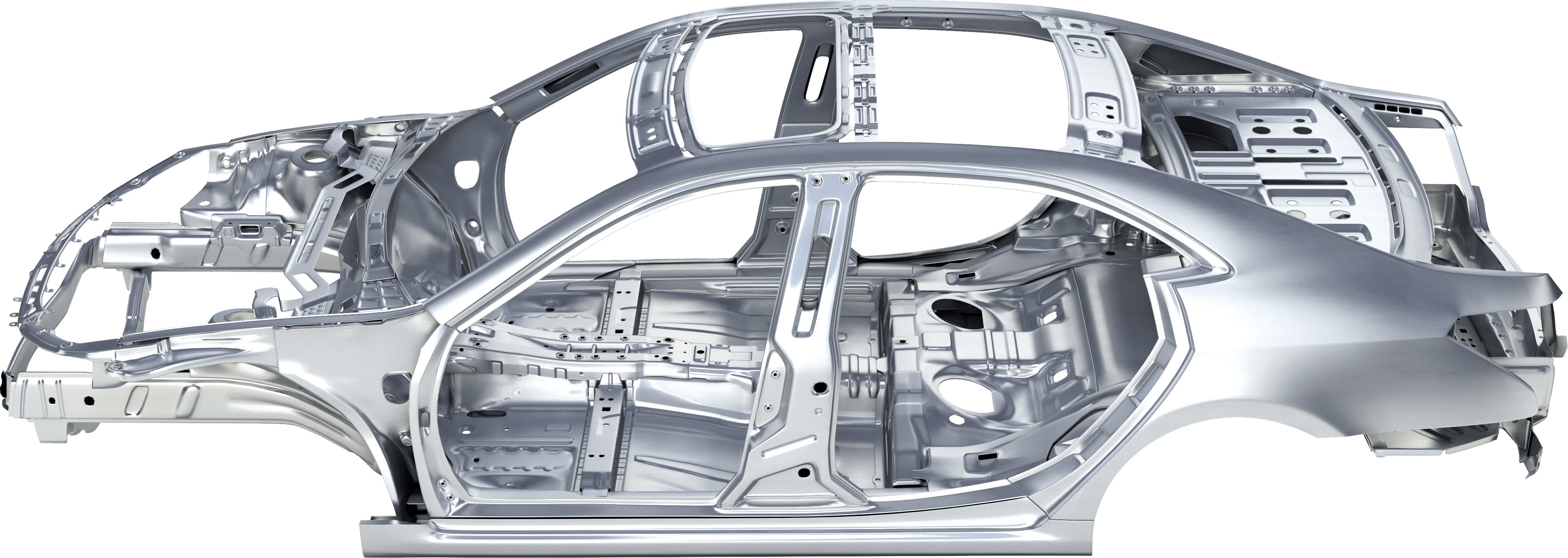
500+
Features Inspected
40 Seconds
Inspection Time
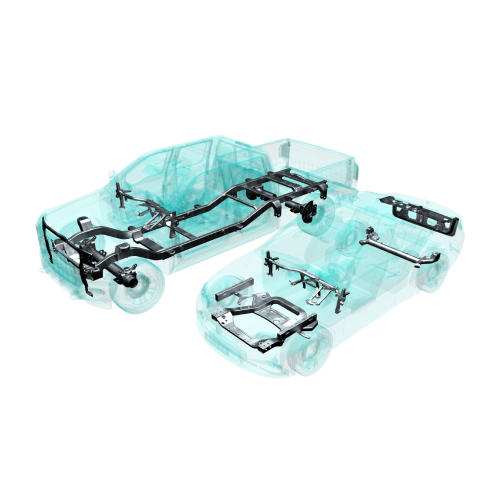
Discover More
With an inspection time of 30 seconds, multi-camera technology enables real-time inspection of all features on each part for automotive body and chassis components.
Learn More About Multi-Camera Technology
In-Line Quality Inspection with Multi Camera Technology
Learn more about how multi-camera technology differentiates from conventional vision systems and how it provides unique benefits for in-line inspection.
Improving EV Component Quality with Multi-Camera Technology
Learn more about how multi-camera inspection technology enables EV battery manufacturers to take full control over quality
A New Paradigm in In-Line Inspection: Multi-Camera Technology
Discover how multi-camera technology works by introducing a completely new technological approach to vision inspection.
Get notified on the latest news from Mapvision
Be the first to know about our advanced solutions by subscribing to our newsletter. Discover how our technology can streamline your workflow, cut costs, and elevate your competitive edge.
Don't miss out—Subscribe now!