In einem früheren Beitrag haben wir beschrieben, wie Ihnen digitale Zwillinge im Kontext der In-Line-Qualitätsprüfung zu einer völlig neuen Funktion verhelfen, die wir mit Virtuelles Sortieren bezeichnen. Weiterhin haben wir die erheblichen betrieblichen und strategischen Vorteile des virtuellen Sortierens für moderne Hersteller hervorgehoben.
Kurz: Virtuelles Sortieren bezeichnet die digitale Qualitätskontrolle von Fertigungsteilen in einer vollständig virtuellen Umgebung. Es ermöglicht interne und externe Sortiervorgänge, die mithilfe des digitalen Zwillings der einzelnen Teile an neuen und vorhandenen Prüfpunkten durchgeführt wird –, ohne dass dazu die Teile physisch vorliegen müssen.
Virtuelles Sortieren macht alle physischen und manuellen Aufgaben in Sortiervorgängen überflüssig und ermöglicht Herstellern ein vollständig digitales, remote durchgeführtes und nahezu zeitgleiches Sortieren. Keine Rückrufe von Chargen, keine eilige Bereitstellung von Ersatzteilen per Luftfracht, keine Kosten für die Sortierung durch Dritte oder im Unternehmen mehr. Dafür senken Sie Ihre Produktionskosten und erhalten weniger Mängelansprüche von OEMs.
In diesem Beitrag zeigen wir Ihnen die Möglichkeiten des Virtuellen Sortierens anhand eines Anwendungsbeispiels in einem echten Szenario.
Der Anwendungsfall: Kunde aus Übersee fordert Sortieren aufgrund neuer Funktion
In diesem Beispiel nutzen wir einen Datensatz von zehn (10) Hinterachsen. Im Szenario haben alle zehn Hinterachsen die In-Line-Prüfung bestanden und wurden an den OEM-Kunden ausgeliefert (der sich am anderen Ende der Welt befindet). In Abbildung 1 sind die Ergebnisse der In-Line-Prüfung für die gelieferten Teile dargestellt.
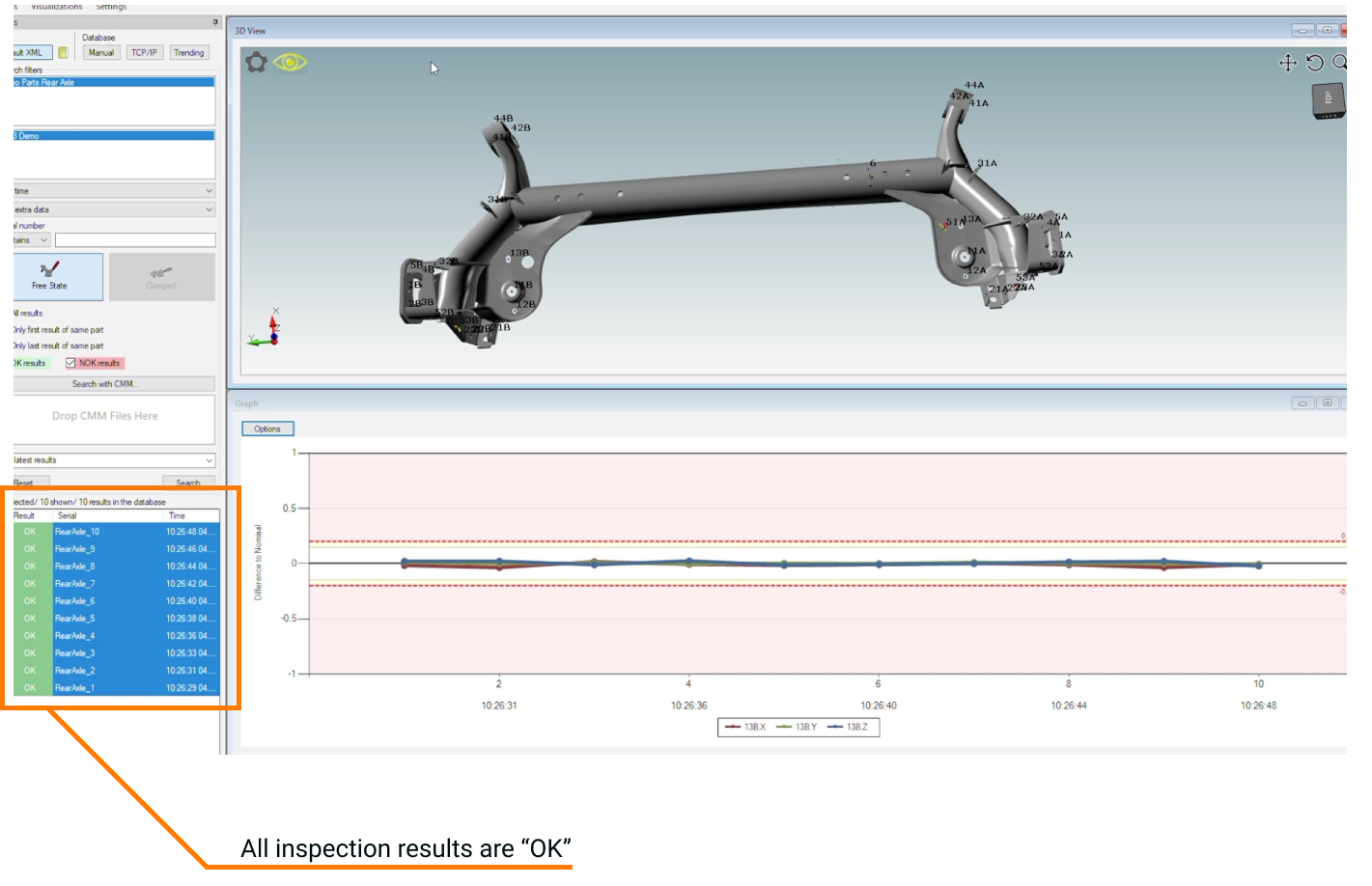
Abbildung 1.
Doch der OEM-Kunde stößt bei der Montage auf ein Problem, das durch den Abstand zwischen zwei Bohrungen auf dem letzten der gelieferten Teile verursacht wird. Obwohl dieser Abstand kein Kriterium in den Anforderungen für die Erstprüfung war und daher nicht im Prüfprogramm aufgenommen wurde, fordert der OEM nun, dass die Teile aufgrund dieses Abstands aussortiert werden. In Abbildung 2 ist der fragliche Abstand dargestellt, der für die Sortieranforderung geprüft werden muss.
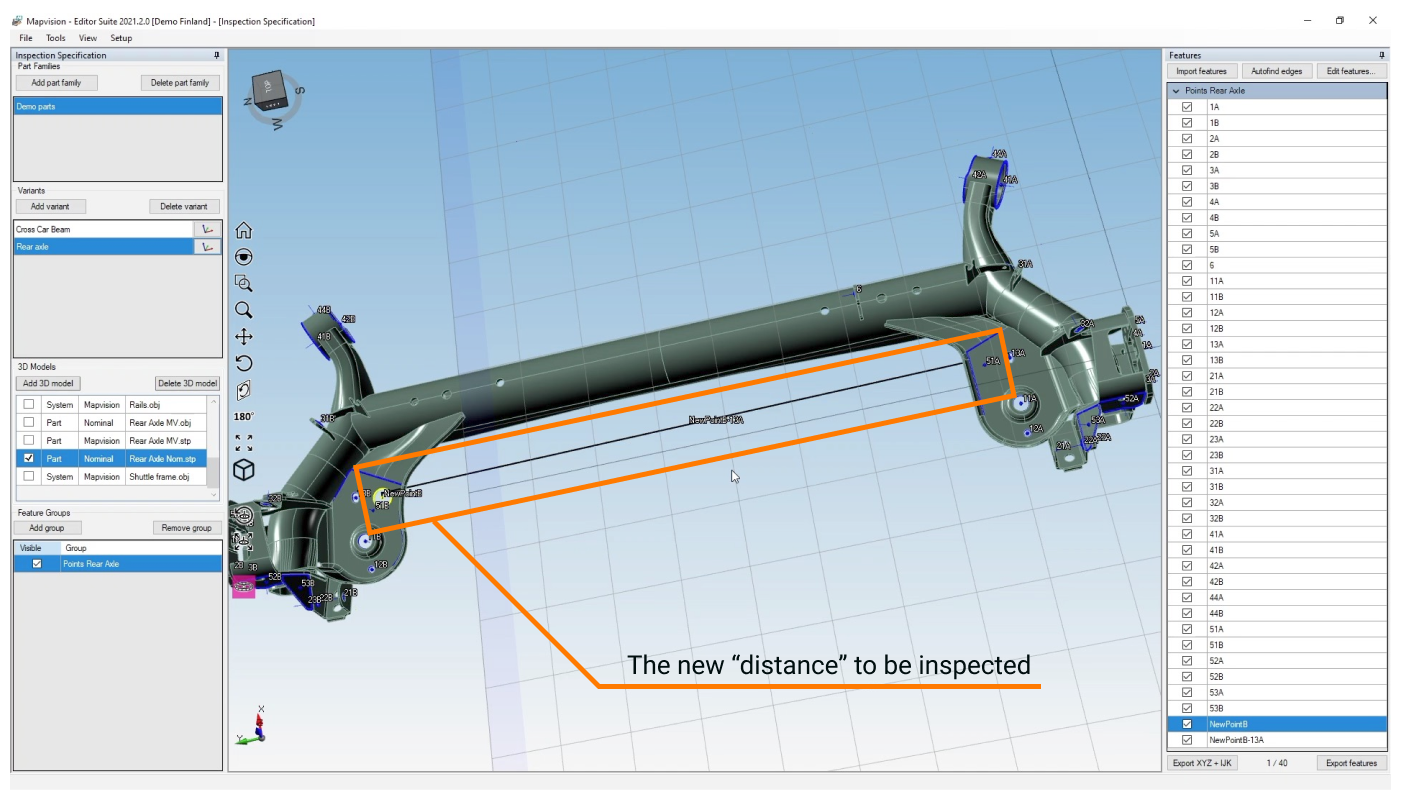
Abbildung 2.
Statt uns auf die Sortierdienste oder Rückrufe von Dritten zu verlassen, nutzen wir Virtuelles Sortieren, um die fraglichen Abstände auf den digitalen Zwillingen des Produkts zu prüfen, die bei der ursprünglichen In-Line-Prüfung erstellt wurden. Anschließend stellen wir unserem OEM-Kunden einfach die Seriennummer der nicht konformen Teile bereit, damit er seine Produktion mit den konformen Teilen fortsetzen kann.
Dazu gehen wir wie folgt vor:
- In der Editor Suite definieren wir den Abstand auf dem CAD-Modell des Teils.
- In der gleichen Software markieren wir den Prüfpunkt für die maschinellen Bildverarbeitungsalgorithmen.
- Wir führen die Prüfung in der Software durch.
- Die Prüfergebnisse werden in Result Suite angezeigt.
Erster Schritt: Definition der Prüffunktion
Sobald uns die Prüfspezifikationen für die Sortieranforderung vorliegen, können wir den Sortiervorgang problemlos starten. Der Bediener kann die fraglichen Punkte für die zu prüfende Funktion einfach markieren – in diesem Beispiel ist es der Abstand zwischen den beiden Bohrungen – und die Spezifikationen für diese Funktion eingeben (Video 1).
Video 1.
Zweiter Schritt: Markieren der Prüfpunkt für die Algorithmen
Nach der Definition der neuen Funktion wird diese in den maschinellen Bildverarbeitungsalgorithmen eingegeben. So können die Algorithmen die Funktion auf den digitalen Zwillingen des Produkts für jedes einzelne Teil erkennen. In der Softwareumgebung markieren wir dazu die fraglichen Punkte auf den digitalen Bildern des Referenzteils (Video 2).
Video 2. Da die neue Funktion als Abstand zwischen zwei Bohrungen definiert ist, muss der Bediener die entsprechenden Bohrungen für die maschinellen Bildverarbeitungsalgorithmen markieren. Dazu wird der Bereich auf dem Bild von jeder Kamera, die auf diese Punkte gerichtet ist, aus „angemalt“. Mit dem Softwaretool lassen sich diese Punkte ganz benutzerfreundlich markieren.
Dritter Schritt: Durchführen der Prüfung
Wenn die Prüfspezifikationen im CAD definiert sind und Sie in den maschinellen Bildverarbeitungsalgorithmen eingegeben haben, wonach Sie suchen, können wir unsere Prüfungen durchführen. Der Bediener drückt dazu einfach auf „Messungen durchführen“ [Namen der Schaltfläche bitte überprüfen] und die Software führt die Prüfungen der gewünschten Teile im Hintergrund aus (Video 3).
Video 3. Die Software führt die Prüfungen automatisch im Hintergrund aus.
Vierter Schritt: Anzeigen der Ergebnisse
Nach Abschluss der Messungen wird der Bildschirm mit den Ergebnissen angezeigt. Wie in Abbildung 3 zu sehen, haben wir aufgrund der Spezifikationen für den Abstand 3 nicht konforme Teile identifiziert. Der Bediener kann eine Liste der Seriennummern dieser nicht konformen Teile exportieren und an den OEM-Kunden übergeben. Dann können die Teile aus der Charge entfernt werden und die Produktion kann mit den konformen Teilen fortgesetzt werden.
Neben dem Export der Seriennummern der nicht konformen Teile sind weitere Analysen der Prüfergebnisse möglich, z. B. die Anzeige der Fehlervektoren oder die Durchführung von Trendanalysen.
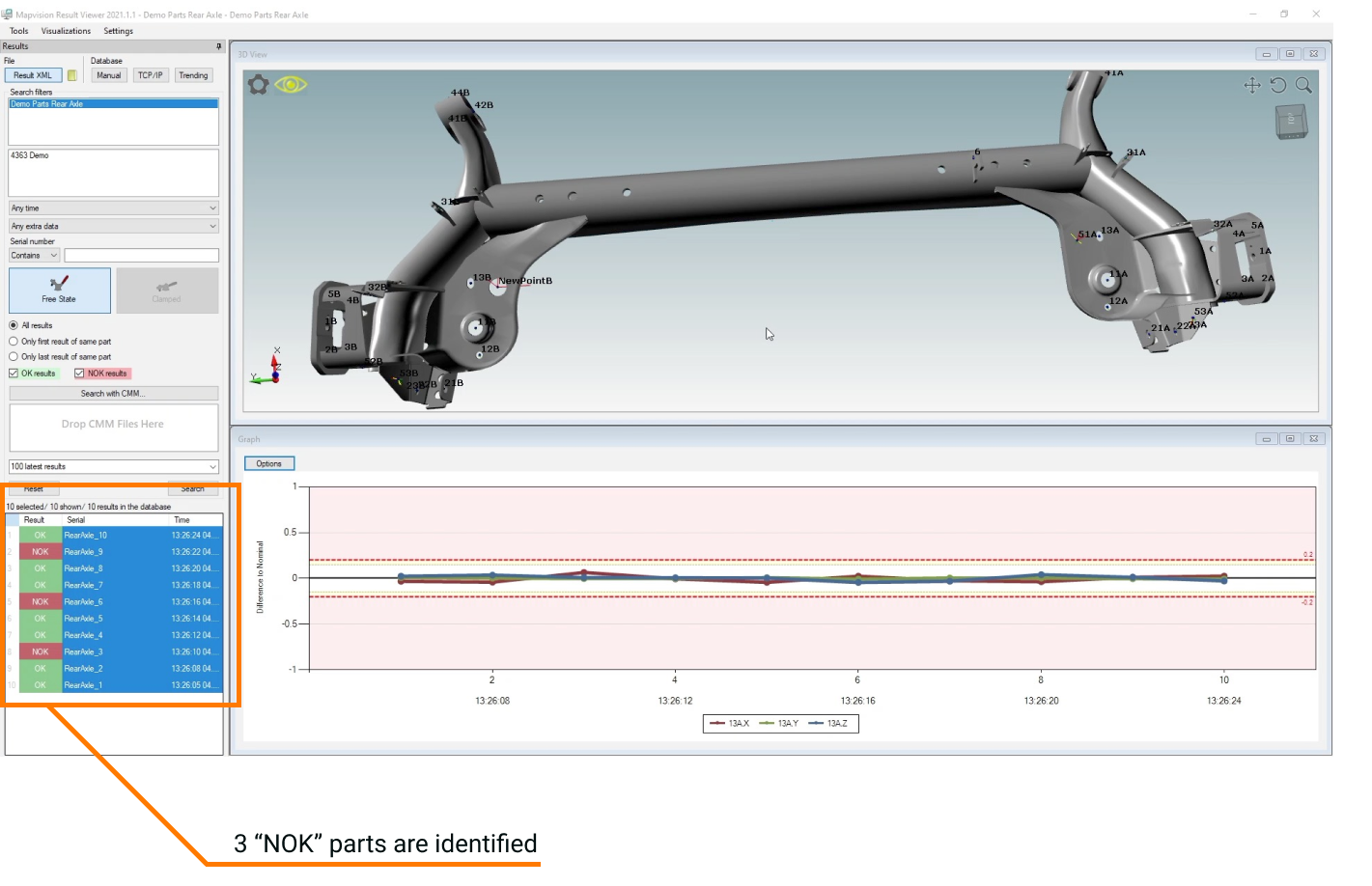
Abbildung 3. Die Prüfergebnisse werden in der Software Result Suite angezeigt.
Visuelles Sortieren – Physische Anforderungen im Qualitätsmanagement werden überflüssig
Manuelle Sortiervorgänge waren bisher eine der größten Herausforderungen im Qualitätsmanagement. Denn Hersteller waren nicht in der Lage, defekte Teile in fehlerhaften Chargen sofort auszusortieren, sondern mussten sich auf teure Rückrufe und die schnelle Bereitstellung von Ersatzteilen einstellen. Aus Sicht der OEMs sorgten Sortierprobleme für schlechte Produktivität, selbst wenn die entstehenden Kosten von den Lieferanten getragen werden.
Große Herausforderungen, für die Virtuelles Sortieren völlig neue Perspektiven im Qualitätsmanagement eröffnet. Es macht physische Anforderungen überflüssig und ermöglicht Herstellern, Sortiervorgänge unverzüglich vorzubereiten, durchzuführen und abzuschließen. Mit Virtuellem Sortieren müssen die physischen Teile gar nicht mehr angefasst werden – ein gutes Beispiel dafür, wie Digitalisierung unsere Arbeitsweisen drastisch verbessern und für neue Effizienzstufen in Fertigungsbetrieben sorgen kann.
Wenn Sie weitere Informationen dazu erhalten möchten, wie Virtuelles Sortieren ihr Qualitätsmanagement optimieren kann, kontaktieren sie uns.